Teamwork leads CU Boulder Racing Team to victory at Formula SAE
The CU Boulder Racing Team recently competed in the Formula SAE student design competition, rising above 101 other university teams from across the world to come in 20th overall.
Put on by the Society of Automotive Engineers, the FSAE competition challenges students to design, build and race a car, all while adhering to a strict set of rules and guidelines that encourages them to create unique and innovative designs within those constraints.
Few expected that the CU Boulder Racing Team, which includes more than 80 members who range from first-year to PhD students, would distinguish themselves this year, since the team was revived just three years ago after a long hiatus.
“Although we’re a new team, we are doing things the right way,” said Project Manager Joshua Hansen, “and trying to the push our university’s name in the right direction in what is a great worldwide competition.”
The four-day competition, which took place this year at the Michigan International Speedway, is a whirlwind event.
The competition is divided into two broad categories: dynamic events and static events. Static events involve technical inspections, presentations and design review, while the dynamic events involve skidpad, acceleration, autocross and endurance tests and races.
“You go from driving the car as fast as you possibly can, and then in 20 minutes, you’re in a design presentation, talking to a judge that knows way more than you do and getting grilled on your engineering decision-making,” Hansen laughed.
And the faster you get through one section or test of the competition, the quicker you can prepare for the next. In other words, time is of the essence.
Watch video of CU Boulder Racing Team's car CB3 in action.
After being one of the first teams to pass the static technical inspection that confirms a car is safe and compliant with the rules and regulations, the CU Boulder Racing Team fueled up their car and brought it to the tilt test. There, judges strapped down their car onto a moveable platform and tilted it at a 45-degree and then at a 65-degree angle, all while a driver was strapped into the seat.
As the judges checked the car for fuel leaks, the test also assessed the weight distribution and center of gravity of the car, verifying that it would not tip over until a specified angle of tilt is reached by the platform.
After that, the team moved on to noise inspection. According to FSAE rules and regulations, every car must be under 98 decibels at idle and under 110 decibels at two-thirds the car’s maximum speed.
At first inspection, the team failed the test. Every team has multiple attempts to pass a test, but it also means the team is slowed down and lacks time and preparation for other parts of the competition.
As the team wheeled their car over to their business presentation, Hansen had one of his team members take the muffler off the car, run it back to the paddock, repack it with fiberglass to dampen the sound, run it back to the business presentation and reinstall it on the car. After the business presentation, the team then wheeled the car back to the noise inspection and passed.
“It’s inspiring to have a team dynamic where everyone is dedicated to having the car perform at its best,” Hansen said.
With so many moving parts, Hansen said clear communication and teamwork were essential to the design and manufacturing processes of building the race car.
“For example, there can be 50-60 people working on the race car at any given time during the manufacturing process,” Hansen said. “It was important that we stayed organized throughout the entire process.”
The design of the race car was organized into three different sections: chassis, powertrain and aerodynamics. If the chassis is the skeleton, the powertrain is musculature system that includes the engine and any component that converts the engine’s power into movement.
Since the FSAE rules and regulations require all engines be under 710 cubic centimeters, every race car uses a motorcycle engine, with most teams using a one- or four-cylinder engine, depending on each team’s strategy on the power/weight ratio of their vehicle.
“Our car is unique because it uses a two-cylinder engine,” Chief Engineer Kayla Ployhar said. “With a two-cylinder, we can see torque across more of the RPM range of the car, while using less fuel at the same time.”
Their strategy paid off during the dynamic events of the competition. “For the acceleration race, we placed 15th out of 121 teams,” Ployhar said. “That definitely proved our theory that we struck the right balance between having a light engine while still having a high amount of power.”
The team also placed 7th in efficiency, 25th in the endurance competition and 45th in autocross.
“It blew me away how well the team did this year,” Faculty Adviser Jeff Knutsen said. “It made me proud that it was my school.”
For next year, the team hopes to develop an aerodynamics package for the car, while streamlining their design and manufacturing process as well. They also plan to lease an industrial space in Boulder that can house their shop and serve as their place of operations.
“I come from the older days of the team when our goals were just trying to qualify at the competition,” Ployhar. “It’s so exciting to see us go from that to being competitive.”
“You can never build the perfect car,” Hansen said. “But it’s that pursuit of perfection that makes it worthwhile.”
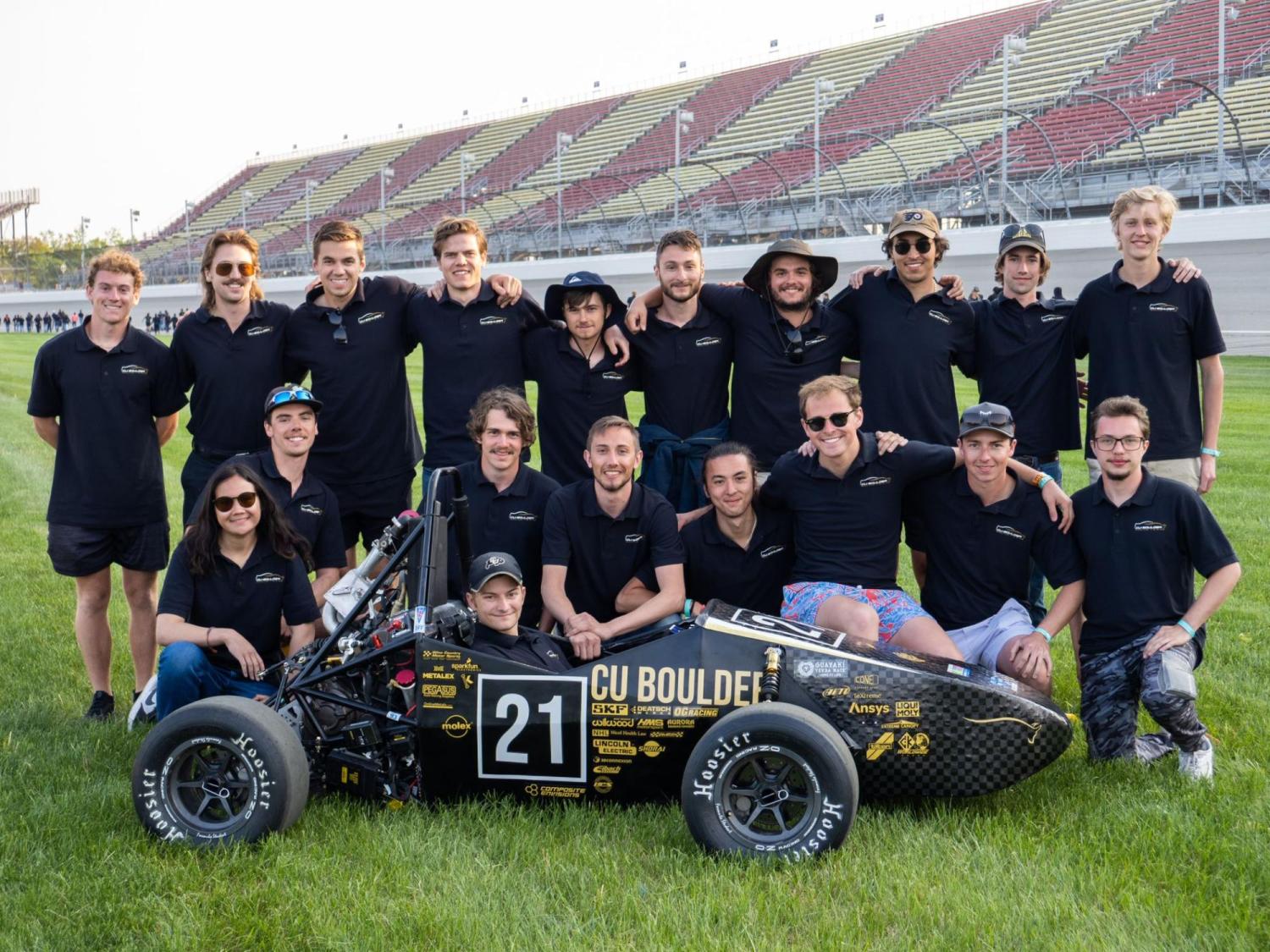