Tougher, Healable Composites through Stress Relaxation at the Resin-Nanoparticle Interface
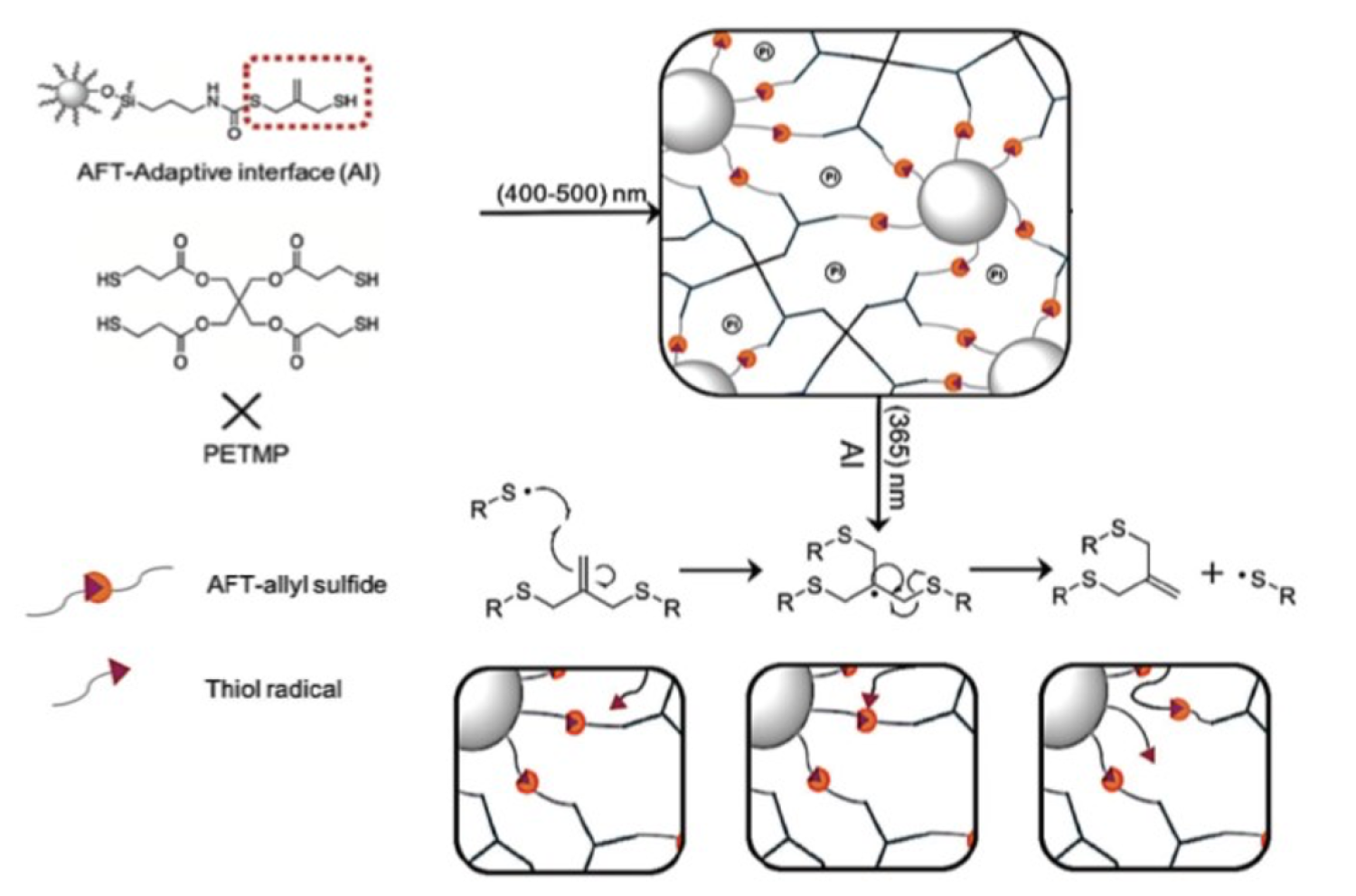
Background
For decades, nanoparticles have been introduced into polymerizable resins to form composites that combine the desired physical and mechanical properties of the constituent phases. However, the interfacial region in composites that incorporate filler materials of dramatically different modulus relative to the resin phase acts as a stress concentrator and becomes a primary locus for composite failure. Since the adhesive strength at the filler interface determines the stress transfer between the components, several techniques have been developed to improve the interactions between the fillers and the surrounding polymer such as bonding the filler to the resin using self-assembled monolayers and surface modification of nanoparticles. While these techniques improve the efficiency of stress transfer at the interface, they do not eliminate the issue of stress concentration or enable stress relaxation. Enabling stress reduction at this interface would dramatically impact the broad field of polymer composites.
Technology
Prof. Christopher Bowman’s research group has employed a new set of dynamic covalent chemistry (DCC) to induce interfacial bond exchange resulting in stress relaxation on demand while retaining a strong, covalent chemical attachment between the matrix and filler phases. The resulting interfacial stress relaxation is achieved with significant benefits to the composite performance, including improvements in toughness, tensile strength, polymerization shrinkage stress, and the recovery of the dissipative energy when subjected to cyclic loading.
Fig. 1: Schematic showing addition fragmentation chain transfer chemistry at filler-resin interface.
Key Results
Silica nanoparticles are functionalized with a silane capable of addition fragmentation chain transfer (AFT), a process by which DCC-active bonds are reversibly exchanged upon light exposure and concomitant radical generation, and copolymerized with a thiol-ene resin. At a fixed particle loading of 25 wt%, the toughness is more than doubled and polymerization shrinkage stress is cut in half in the adaptive interface (AI) composite relative to otherwise identical control composites. In situ activation of the AI during mechanical loading results in 70% stress relaxation and 3x higher fracture toughness than the control. When interfacial DCC was combined with resin-based DCC, the toughness was improved by 10x relative to the composite without DCC in either the resin or at the resin–filler interface. For additional results, see Adv. Mater. Interfaces. 2018, 5, 1800511.
Advantages
- Higher filler loading (beyond 15%)
- Lower shrinkage stress and improved mechanical properties
- In-situ stress relaxation
- Reduction of the number of voids sites in composite
Applications
- Polymer composites (coatings, structural materials, dental materials, etc.)
What's Next?
This technology is available for exclusive or non-exclusive licensing.
Nicole Forsberg: nicole.forsberg@colorado.edu
The Newsroom
For marketing and communication inquiries or news tips, contact Daniel Leonard, senior marketing and communications specialist for Venture Partners at CU Boulder.
For media inquiries, please visit colorado.edu/news/formedia.